KIH[Purist]
12044
Japan's new old Brand: Factory Visit to MINASE - True Qualification
Apr 15, 2014,19:13 PM
Factory visit report - MINASE [mi-nah-sei] : Japan's new old brand with true qualification.
I
was fortunately invited to MINASE factory together with others -
including a watch journalist, PR specialist, and a photographer. Minase
is trying to notch up its brand image and get to the next level to get
widely accepted and respected as a manufacture watch brand. But the
truth is that Minase is already doing quite well in the watch making in
Japan, just that fact is very little known.
0. Factory and surroundings

The
nearest station - Yuzawa Station (about an hour ride from Omagari
station where we got off Tohoku Shinkansen or bullet train, to which it
takes 3 and a half hours from Tokyo Station, at the speed of 320km/h).
And from this station, it takes again about 30 minutes to the factory -
quite a trip, but well worth it.

Reminded me of the road from Geneva to Valle de Joux....

The factory houses 26 workers. With no brand or sign of the watch factory....

At the entrance of the factory. HiZ series, VY03.
1. Let me start from its history.
The name of the company is Kyowa Precision
, a precision tool manufacturer, founded in 1963 by Mr. Kouichi
Suzuki. Kyowa developed the special "step drill" to be used to open the
hole for the crown of the watches and it sold quite well to the big
watch brands. And then, those watch brands started asking Kyowa to make
the watch cases altogether including of course drilling the hole for
the crown stem. Along the way, Kyowa acquired the skill set for the
high-end watch case making.
The time flies and the watch brands
shifted case subcontractors to other countries. It was sort of a
"crisis", but Kyowa then decided to make watches by themselves with the
skill set they already possessed (except for the movement). Kyowa built
the watch factory in Minase, Akita prefecture (north western part of Japan) in 1988, and the name of the location - Minase - became the brand name.
Aside from MINASE brand watches, Kyowa provides OEM watches to several
fashion and jewelry brands (cannot mention the names here, but you would
be surprised.... both mechanical and quartz) and that is doing quite
well.
The advantage of Kyowa/ Minase is clearly the precision tools they make - Even
a few very, very big and respected Swiss watch brands buy their
tools! Again, you would be surprised at who use Kyowa/ Minase
tools.... Also note that Kyowa has its tool manufacturing factory nearby, where we did not visit this time.
2. How they make the cases - forging, honing, polishing, buffing and finishing.
(1) Forging:
They have various press machines -


160 ton machine x 2
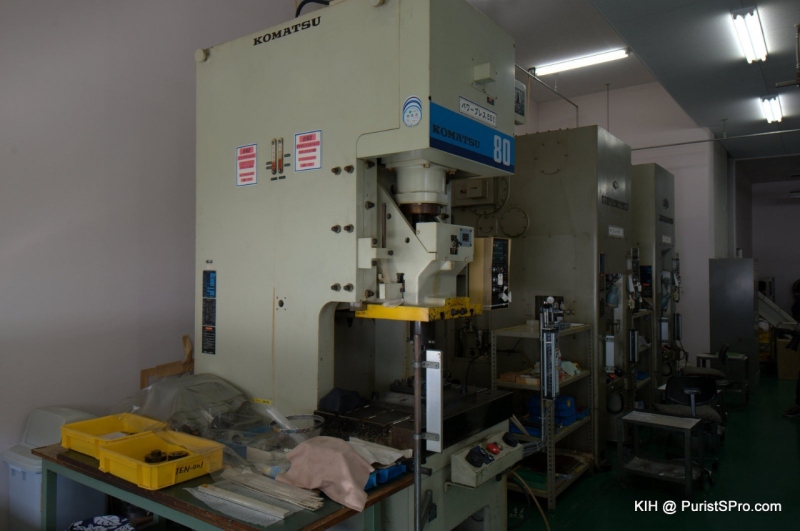
80 ton x 1

35 ton x 2
The actual forging. This is the 7th time of these cases (the photos show OEM watch case making) out of total 13 to 15 times.

At the load of 72 tons!




And then they are brought to the heating machine
(1,120C) for 20 - 25 minutes. Then go back to the press machine -
repeats 15 times.


These machines may all look pretty old, but for small quantity order, older machines are more efficient to adjust and handle.
(2) Polishing
This is the model whose case and other parts are polished as shown below. Interesting design called "Case in case" structure.
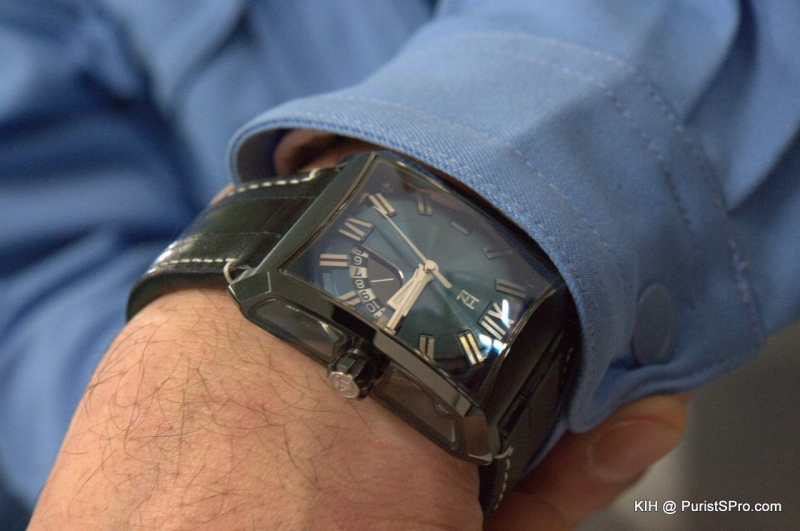
First stage - raw after forging.

Second - a bit of softening the rough edges.

Third - after honing.

Fourth - After Salaz polish on the top surface (bezel)
(*
"Salaz" was the name of the polishing machine brand which has been
widely used by the case makers, thus now the name "Salaz" is used as one
method or process of polishing)

Fifth - After buffing the top surface

Final - all 14 surfaces (!) after Salaz polish and buffing. Sharp edges are intact.

The final one from the side - mirror like surface with
sharp edges left: extremely time consuming process. Needless to say,
the holes on the side and the crown are done with Kyowa tools.

Left half is after Salaz polish only, the right half is after final buffing.

Polishing Machine


Salaz
polishing (polishing against the hard board of file - three times for
each surface, from rough to fine) - leaves the sharp angles.
Index part of the above model.



The dial inside - the process for polishing this part is even more jaw dropping.
a. Honing the surface
b. Polish the fan-shape date window with the leutor by hand
c. Salaz for the chamfering (0.7mm width), and then hair line finish for the outer dial and the side.

(3) Other notable equipment
Electrical Discharge Machine and Wire-Electrical Discharge Machine
have been used since 1985. Some Swiss brands just started using this
type of machines.
They make their own metal mold here.

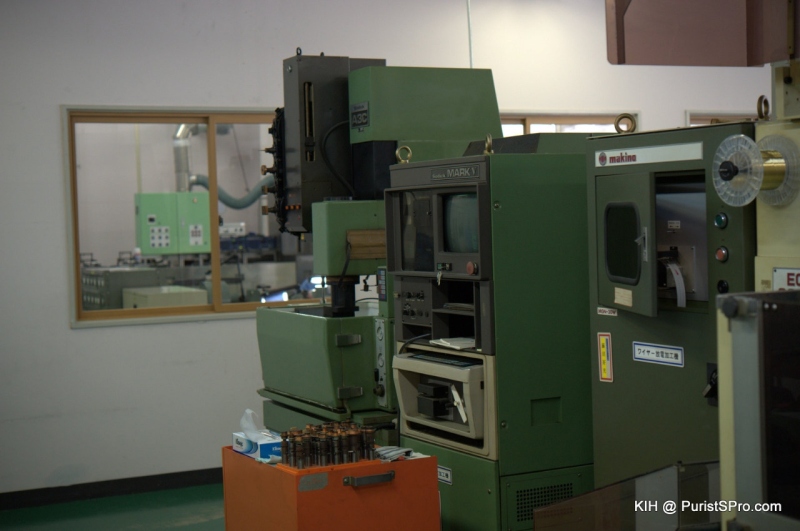
3. Putting the sapphire glasses on the case

Syringe is used to put on the special UV glue.

Then use Q tips to apply the glue equally

These are all the Sapphire glasses to be put on the case...

Finished.....
4. Assembling the "case in case"



Putting the hands on it....



5. Perlage
Not just another ETA2824. Spare no time and effort.

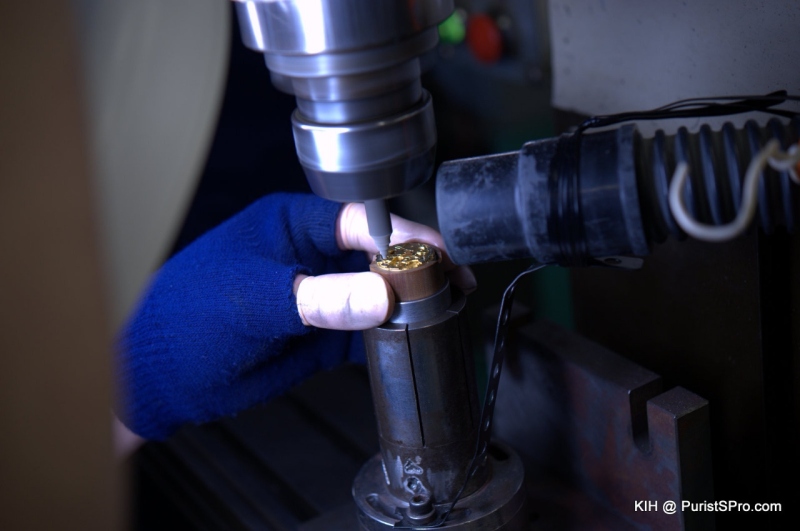

After

Before
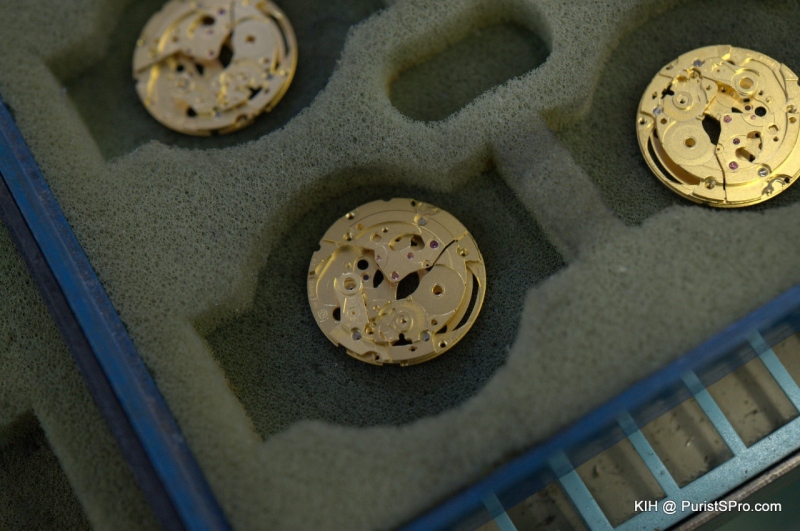
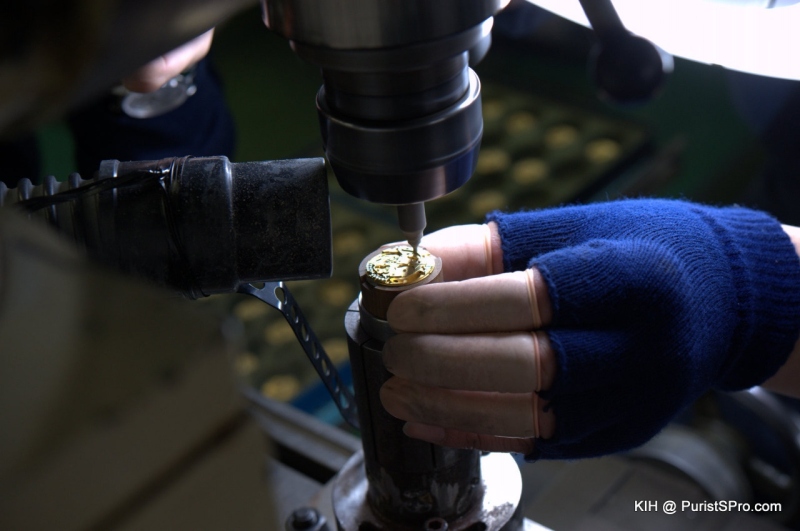
End of Part 1
Please read Part 2 for their models, and Part 3 for the interview with the Brand CEO, in-house movement.
=============================================================================
Please read and comment here=>
home.watchprosite.com
This message has been edited by KIH on 2014-04-15 19:14:09
Comments:
view entire thread
Japan's new old Brand: Factory Visit to MINASE - True Qualification
By: KIH : April 15th, 2014-19:13
Factory visit report - MINASE [mi-nah-sei] : Japan's new old brand with true qualification. I was fortunately invited to MINASE factory together with others - including a watch journalist, PR specialist, and a photographer. Minase is trying to notch up it...